Five Myths on Carbon
Even if carbon has now been used for many years to produce frames by most companies in the bike industry, the material and the way it is used remain a mystery to many. Because we manufacture performance bikes and our expertise in composites is now well recognized, we are regularly asked questions on the subject. So, as we approach Kona, we thought it was time to review some of the myths surrounding composite bike frames.
1. Are carbon frames really made of carbon?
Let’s make things clear: there is no such thing as a carbon frame. What everyone refers to when talking about a carbon frame is actually a composite frame made with carbon fibers.
Carbon fibers alone are, like the word says, fibers. To build a high-end composite frame, bike companies will use mostly unidirectional [UD] fabric made of carbon fibers pre-impregnated with an epoxy resin*. This pre-impregnated fabric is cut into patches that are placed strategically in multiple plies onto a bladder. Once this is done, the bladder is set in a mold. The mold is then heated for the composite to cure. Without epoxy resin, there would simply be no frame.
It is important to understand that depending on the model and level of bike frame produced, different types and grades of fibers can be used, some of them unidirectional, others weaved. For instance, glass fibers are commonly used along with carbon fibers in the fabrication of entry-level composite frames to control production costs. Even high-end composite frames are made of different grades of carbon fibers combined according to design, performance and safety requisites.
*Epoxy resin is a type of plastic material widely used in the composite industry

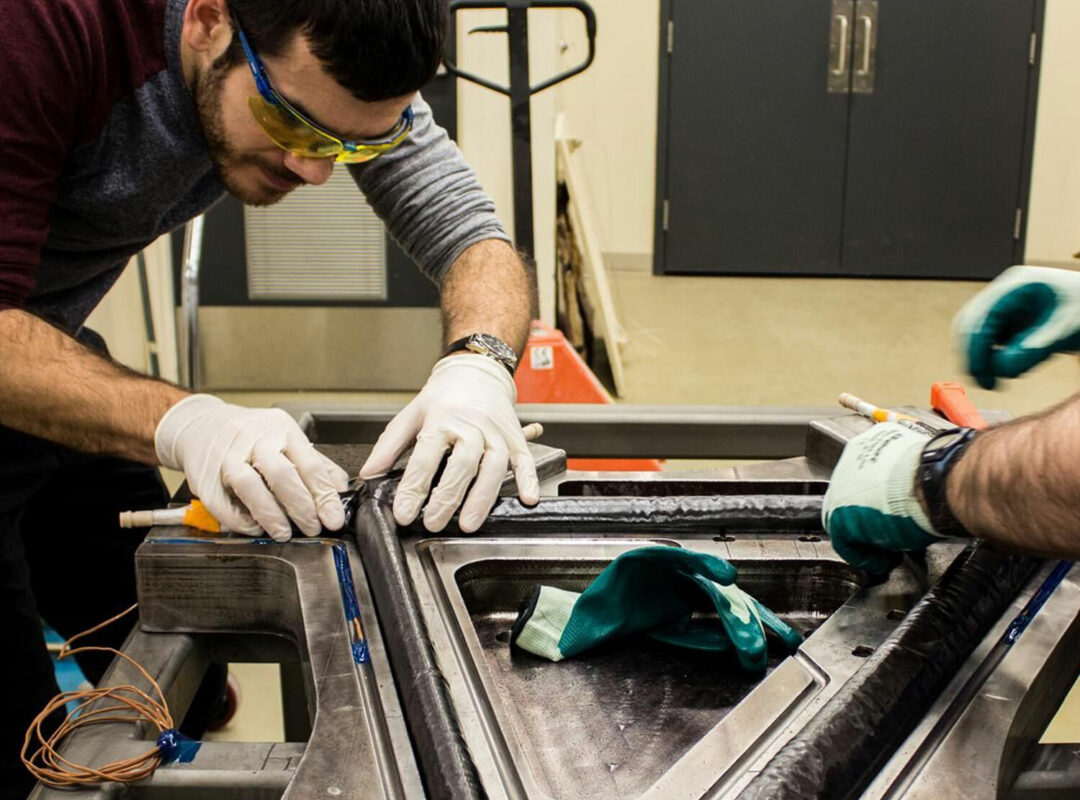
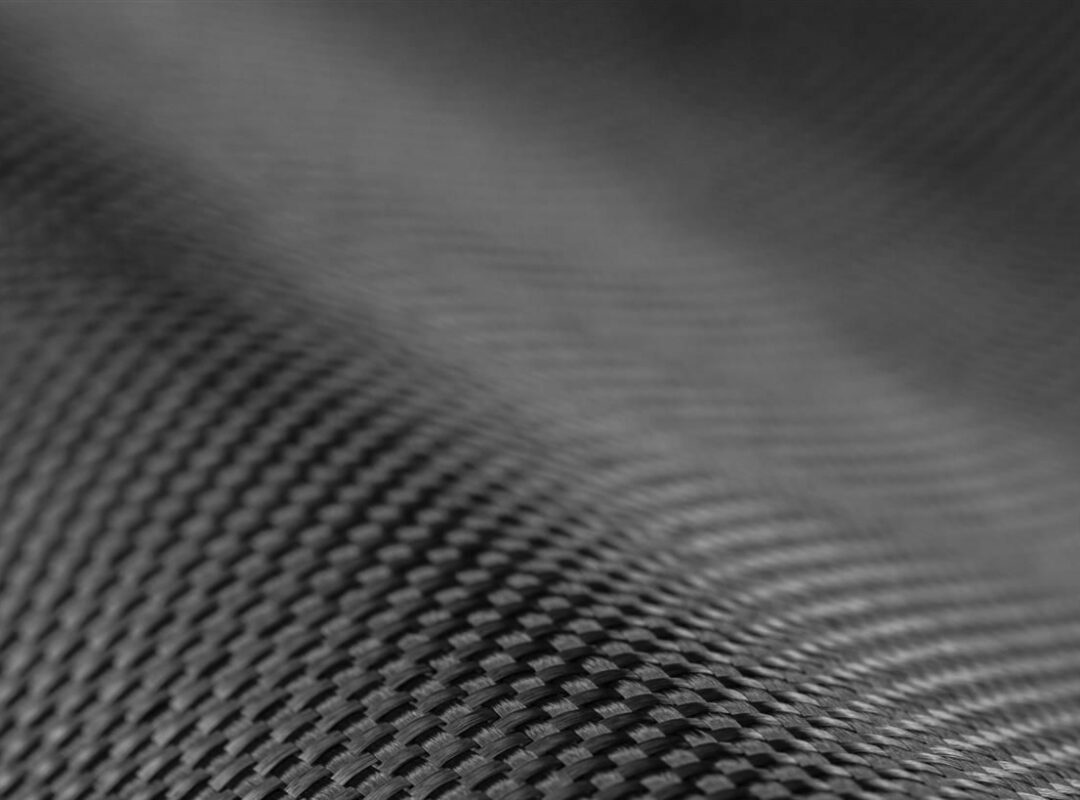
2. Composite frames are less comfortable than titanium, aluminum or steel frames.
There is a lot of talk on what material makes the most comfortable bikes. When manufacturers started experimenting with composite frames some forty years ago, they saw it as an opportunity to make stiffer and lighter bikes than previously possible with metal frames. These early generation composite frames transmitted road-induced vibrations to riders in ways that gave them a reputation for being uncomfortable. Nowadays, with all the expertise garnered over the years, bike manufacturers like Argon 18 control the level of stiffness of their frames making them very stiff in certain areas where rigidity is needed and more flexible in other areas where comfort is more important. This is possible through tube geometry and fine tuning of the carbon lay-ups*. Therefore, composite frames are no less comfortable today than frames made of any other material traditionally used for their production.
* For each composite ply, the lay-up is a detailed set of instructions on the ply position, fiber orientation and type of material to be used in the manufacturing process.
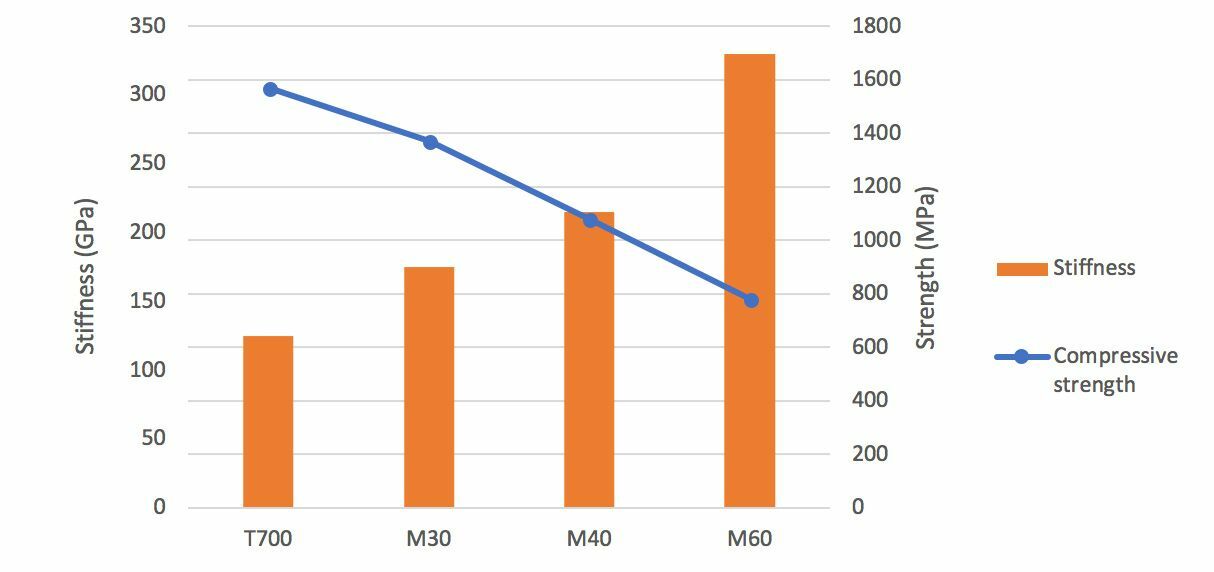

Let’s make things clear: there is no such thing as a carbon frame. What everyone refers to when talking about a carbon frame is actually a composite frame made with carbon fibers.
R&D - Argon 183. High-end composite frames require significantly longer manufacturing times because they are made up of more carbon folds.
There is no easy answer to this one, but generally speaking, manufacturing times are very similar for both entry-level and high-end composite frames. Carbon plies, expensive high modulus or entry-level grade, are applied by hand. High-end composite frames are usually made using less carbon plies than entry-level ones, but these plies must be positioned very precisely to prevent defects that could prove problematic for frame performance in both stiffness and safety. As stated earlier, entry and mid-level frames are made using more carbon plies. On average, the front triangle of a composite frame is made of about 120 plies, all placed by hand which is a time-consuming operation. So, in the end, the manufacture process takes pretty much the same time to complete whatever level of composite frame one is building.
It is in the design phase that high-end frames require a lot more time to develop than entry level ones. The amount of R&D involved in the conception of a high-end frame in order to meet all design requirements cannot be matched by that of entry or mid-level frames considering that, in most cases, these entry and mid-level frames benefit from trickled down technologies, geometries and designs coming from the top of the line models.

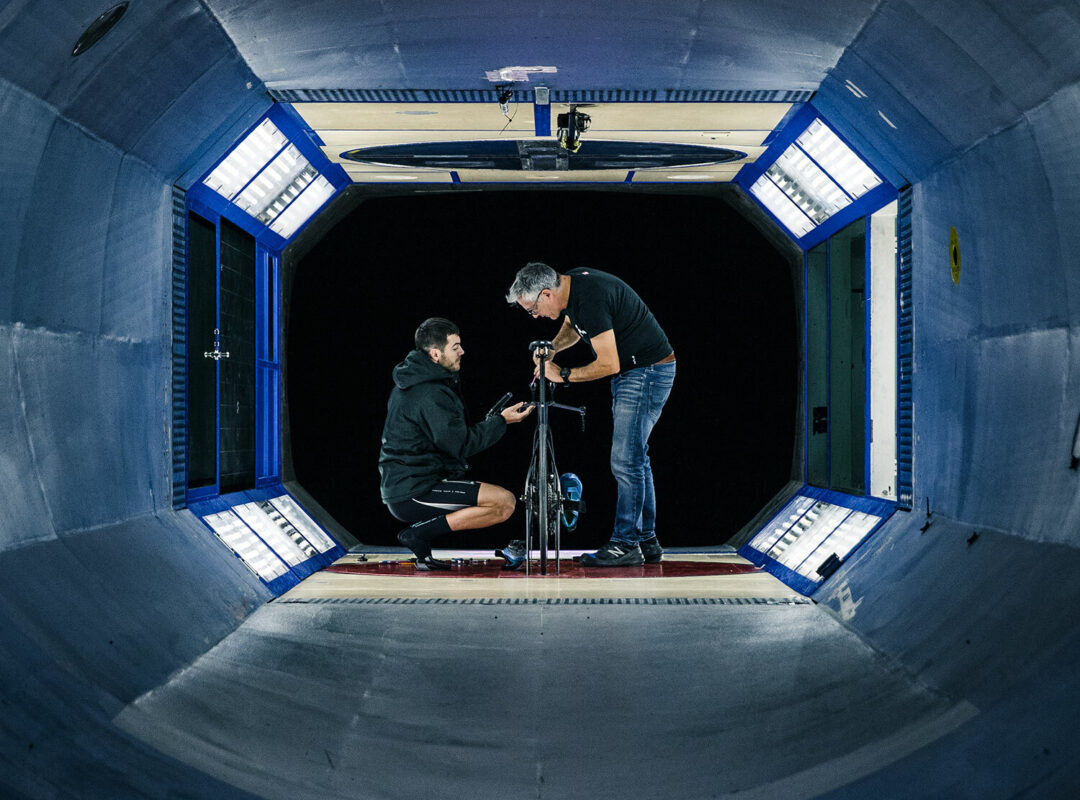
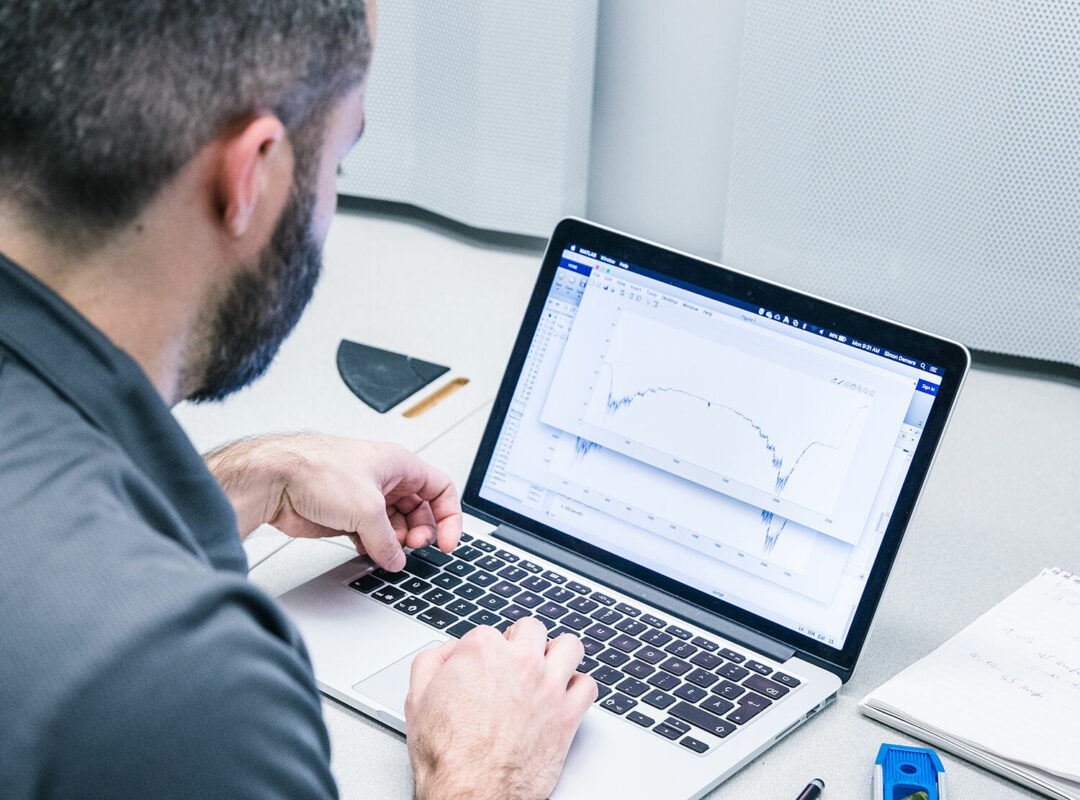
4. Lightweight composite frames are built using only the most expensive carbon fiber.
Again, this is more myth than reality. Although it is safe to assume that the stiffness-to-weight ratio of the most expensive carbon fiber is higher than that of an entry-level one, it does not mean that expensive carbon fibers are in any way lighter than less expensive ones. They are stiffer and more brittle so if one was to build frames using only the highest grade, most expensive carbon fiber available, it would make stiffer and most probably lighter bikes. But those bikes would also be a lot more fragile. A compromise needs to be made in order to build true high-end bikes that can be ridden in normal, everyday use.
The design of lightweight high-end composite frames requires a complex blend of different types of carbon fibers intricately laid up in a way to meet all design requirements and pass all safety tests. These safety tests are the same for all levels of bikes and are defined by international standards (ISO standards). The design of high-end, lightweight composite frames requires a level of expertise and know-how that only comes with years of experience with composite bike design and manufacture.
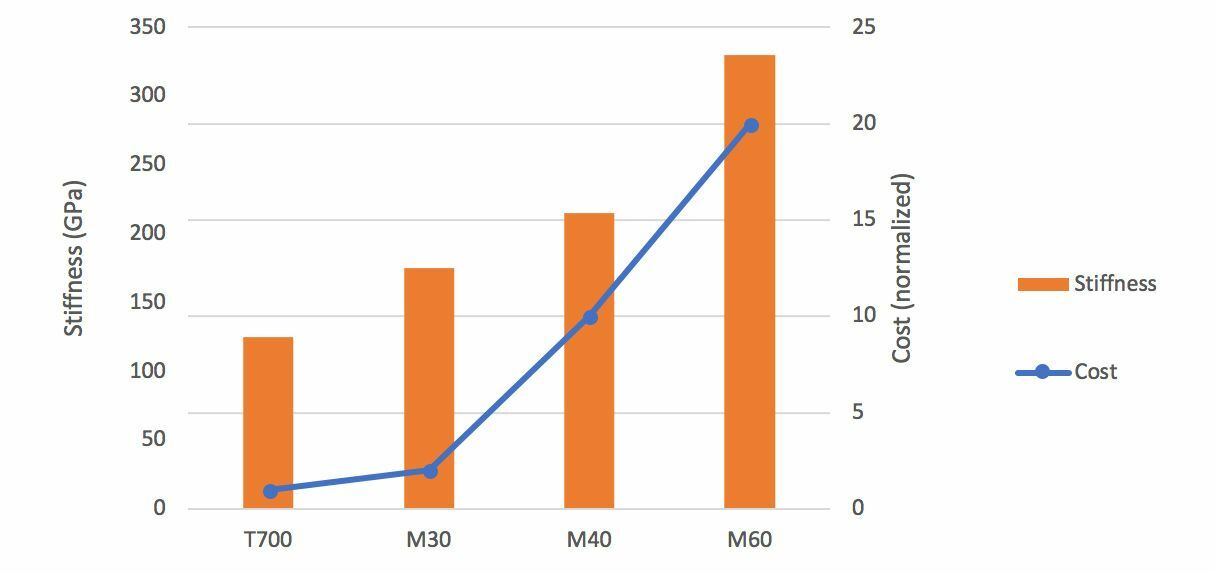
5. Composite frames lose their riding characteristics over time.
All materials, aluminum, steel and composites alike, used in the fabrication of bike frames will lose some of their characteristics over time due to repeated stress. In order to prevent this, all Argon 18 frames undergo fatigue tests so that the company can develop carbon recipes and fabrication techniques that will render this so-called degradation imperceptible to the rider. An Argon 18 frame model will only go to production if its stiffness and resistance values respect norms set by Argon 18 for test approval. These norms are significantly higher than what a frame will ever be subjected to in reality.