Our Approach: Testing
The safety and performance quality of our bikes is our largest priority. Our testing and quality control protocols are among the most rigorous in the industry, and we are constantly adding to or augmenting our test standards to ensure the best possible experience for our riders.
Overall, our testing falls into two main categories: performance requirements and safety requirements. Safety requirements are industry-wide standards. Often these are set by ISO guidelines (International Organization for Standardization), although we have developed and implemented additional tests where we feel appropriate.
Performance requirements include assessing the benchmarks we set for each bike, such as weight, comfort, handling, stiffness, and aerodynamics, among other performance benchmarks. Unlike safety tests, these tests produce discretionary results, based on targets that we have set for ourselves. Examples of performance testing include stiffness tests and vibration tests. These tests help us benchmark the frame characteristics required to achieve the desired performance qualities in each specific model. For example, on a track bike where we wish to achieve high levels of power transfer, we’re looking for high stiffness at the bottom bracket area. For an endurance bike, we’ll want to measure vibration tests to limit road feedback on long rides.
Safety tests
Safety tests take several forms to be sure we test all possible parameters and meet all international safety standards. We undertake static, fatigue and impact tests to simulate possible stresses on the frame. In static tests, a load is applied to the frame and maintained during a short time. In fatigue tests, a load is applied under repetitive movement. In impact tests, a weighted striker is dropped on the frame, or the frame is dropped with weights on it.
Most tests are determined by ISO standards. However, in some cases we use additional measures that go beyond these standards. Some examples of these additional tests are:
- For gravel bikes, we have added rearward impact tests to account for the specific use of these bikes;
- There are currently no standardised requirements for rear disc brakes, so we have added tests for this, as well as for steerers;
- For track bikes, the load applied by sprint riders on the pedals can be more than three times higher than ISO requirements. We’ve developed new tests for track bikes to match this level of power output.
- Frame:
- Bottom bracket stiffness
- Chainstay stiffness
- Headtube stiffness
- Seatpost stiffness
- Frontal vertical stiffness
- Fork:
- Frontal stiffness
- Lateral stiffness
- Seatpost:
- Vertical stiffness
- Handlebar and stem:
- Lateral stiffness

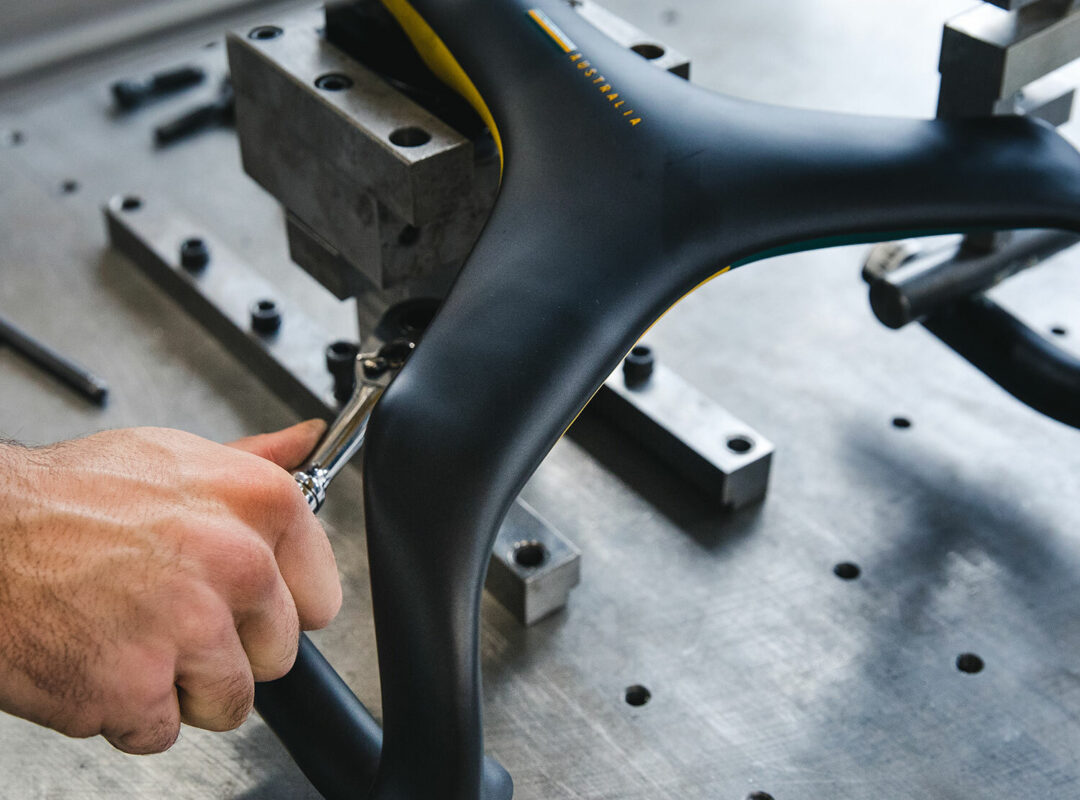
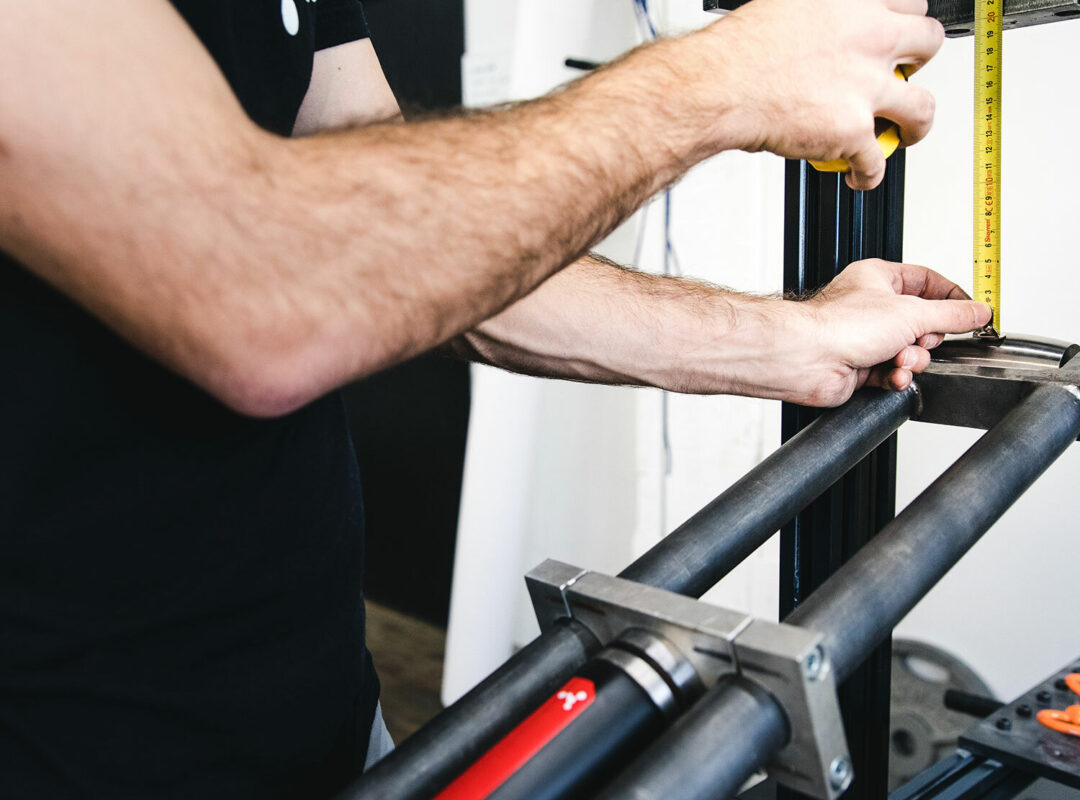
Performance Testing: Stiffness Tests
Stiffness tests measure the deflection on the frame under load. A stiffer area of the frame will measure little deflection; a more compliant area will measure higher. A load is applied to a specific point of the frame and fork, and deflection is measured. The most common stiffness tests include:
As a generalization, we can equate certain stiffness tests with performance parameters. For example, some common assumptions are:
Bottom bracket stiffness = pedaling efficiency
Head tube stiffness = precision handling
Chainstay stiffness = pedaling efficiency
Seatpost compliance = riding comfort
In reality, the relationship between stiffness and performance is not quite so linear. However, these generalizations are useful in understanding why we test certain aspects of the frame.

Performance testing: Vibration Tests
How do we test for comfort?
Comfort is highly subjective, therefore has traditionally always been difficult to measure. Very frequently the experience of riding comfort is influenced by things other than the frame: tire size and pressure, wheel choice, and saddle, among other factors. However, Argon 18 has developed a unique way to gather more information about comfort as it relates to the frame itself.
To test for comfort, we have to understand the actual stresses and strains on a bike under real riding conditions and then use that data to simulate those conditions in the lab. We use a bike outfitted with strain gauges and accelerometers in order to collect this information through real-world riding. We then use a second bike in our R&D lab where we simulate these vibrations that are experienced on the road, using a testing platform fitted with the same equipment used in 4D cinemas to make the seats vibrate. We then measure the acceleration on the saddle and stem using accelerometers, and the deformation of parts of the bike such as the handlebars and seatpost. Less vibration power recorded at those contact points means less vibration – so more comfort for the rider.
This type of test gives much more accuracy into the parameters of comfort than simply relying on a vertical compliance test. Vertical compliance is linked to comfort, but it is in no way directly proportional, nor are all vibration frequencies themselves relevant to compliance. When we are able to directly measure the power that’s going into the frame from the vibration of the wheels, we can have a better sense of what the rider will actually experience on (or off) the road.
