Our Approach: Prototyping
Prototyping is a key stage of our development process where we produce a physical model to validate or further investigate our design intentions. We use prototyping as part of two key processes: our bike development, and our advanced research projects.
There are several major reasons why we produce prototypes as part of bike development:
- To test real-world functionality: we test the performance of design features such as integrated cables or component compatibility, or to be sure the bike’s assembly will be mechanic-friendly.
- To continue performance testing, such as the wind tunnel testing described in our article on aerodynamics, which is often undertaken with a prototype.
- To undertake safety testing.
To test real-world functionality, we often use our in-house 3D printer to produce a prototype which is true to the design of the bike, but of course, not rideable. This process allows us to be more efficient in design iterations, especially in the early stages of design. For example, if our designers want to test specific tube shapes both for design quality, general aesthetics, and for functionality, we can print an isolated section of the bike, such as a tube junction. We can also test compatibility with different components at this stage, such as derailleur mounts, internal cabling, or tire clearance.
We can undertake efficient performance testing with this same approach of printing selected areas of the frameset. For example, we’ve taken an early prototype 3D-printed fork to the wind tunnel and ran tests with it mounted on an existing frame, to benchmark aero improvements. We took this even further in the development of the new Electron Pro in partnership with Cycling Australia and researchers from the University of Adelaide. During the development phase, we produced a modifiable prototype, with interchangeable plastic versions of several key areas of the frame under development, such as the seat tube and top tube junction, headtube, and the fork. We were able to effectively swap slightly different shapes in order to test, identify and move forward the design option that provided the best results. We were able to efficiently test each of several design concepts with one trip to the wind tunnel, by simply swapping out these key areas on the frame.
Another part of prototyping is testing the interface between the composite frame and the individual plastic parts that will need to fit onto the frame, such as the modular cable console on the Krypton, or the caps for the 3D+ system. These parts require a precise fit to deliver efficient and user-friendly performance, so testing their fit is crucial.

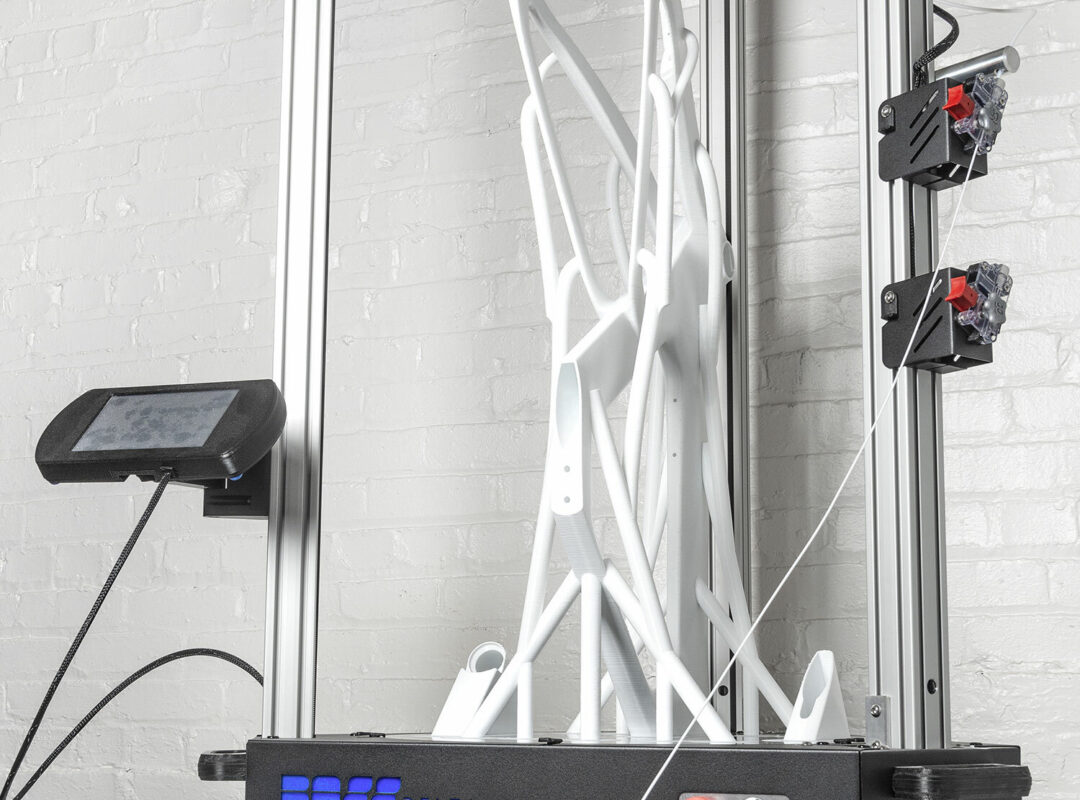
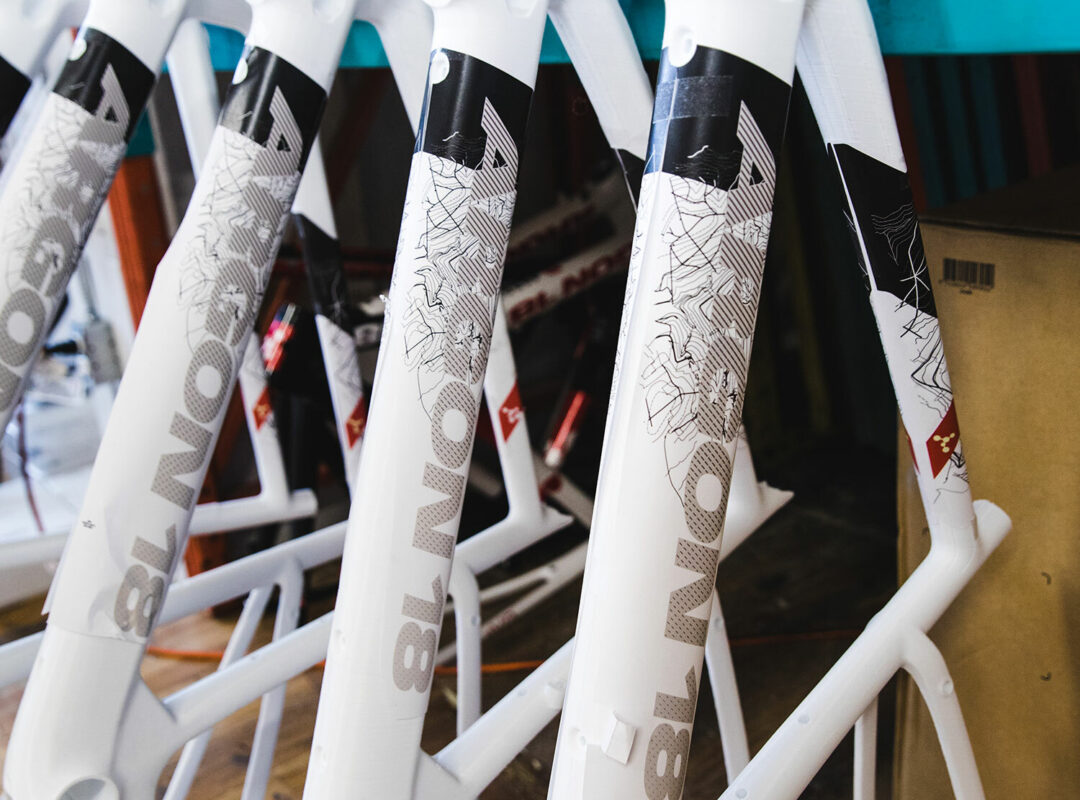
Validation
This early prototype testing takes place before we create the mould for a bike frame. Once we have the mould, we move into the stage of validation of the frame. Two early sample sets are made: looking samples and riding samples.
A looking sample allows us to check the quality of the mould. We will be able to see if the surfaces of the frame are smooth, the tube shapes are accurate, and if the fit with required plastic parts is compatible. We are also able to test artwork at this point, to be sure the final product will be produced true to the design intentions.
The riding samples undergo more rigorous testing, such as stiffness and fatigue tests, which we describe in more detail here. Other riding samples – much as the name implies – are used for field testing. We fully assemble a bike and often have our pro athletes test it and provide feedback on how the bike handles in real-world riding conditions.
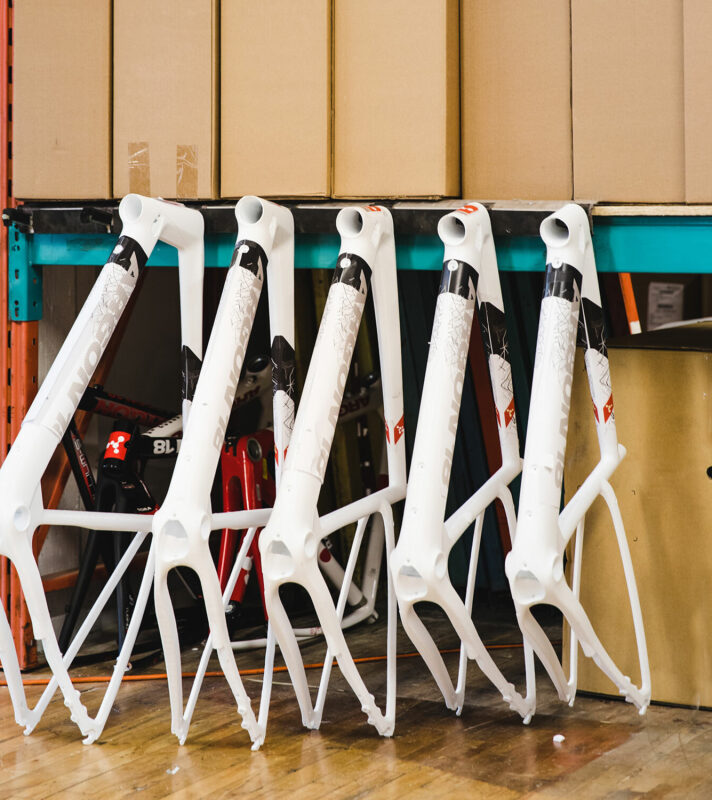
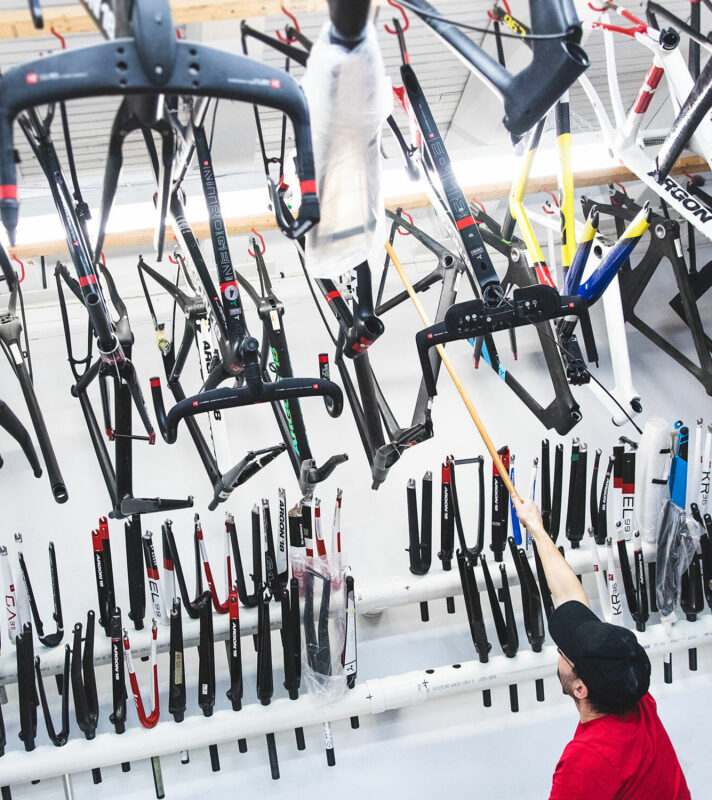
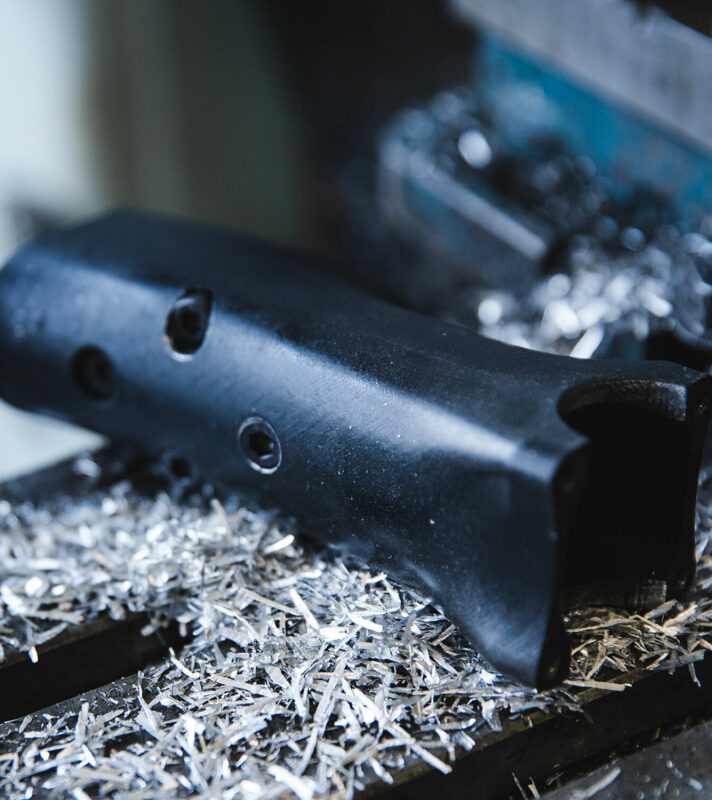
Prototyping as Part of Advanced Research
We also use prototyping as part of our ongoing advanced research programs. In this research we may not be working on one specific model, but rather looking to gain new knowledge on the behaviour of certain areas of the bike frame, or further develop our expertise in composite engineering.
Much of our advanced composites research is done with the Composites Development Centre of Quebec (CDCQ). When we create composite prototypes as part of our research, we are able to increase our understanding of the entire manufacturing process, from developing the layups and moulds through to the final product. We are now in the stage of trying new materials and methods, and new approaches to layup.
In our hands-on research work we are able to find cost-effective methods of design and development validation, for example, by manufacturing and inspecting just one tube at a time, something we would not be able to do as efficiently if we were working with a distant factory. This speeds up the development process and allows for targeted engineering. We can see firsthand the successes and irregularities in the production process, and adjust our designs based on this end-to-end product knowledge.
This advanced prototyping work ties directly into the manufacturing stage of our process. When we propose new methods to our partners in our manufacturing facilities we are able to do this based on our own hands-on experience with the techniques of production. This makes our working relationships more efficient, and adds a level of collaboration that helps us provide the best possible products to our riders.